What is Die-cut Tape? Comprehensive Analysis
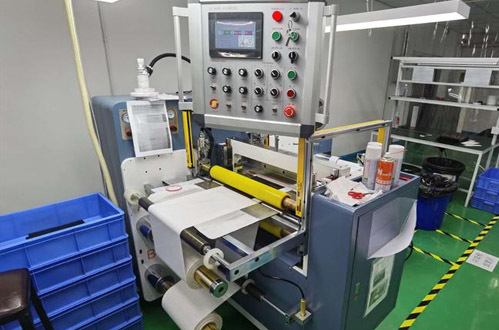
Die-cut tape is a pressure-sensitive tape that is precisely cut into specific shapes and sizes, such as gaskets, seals, mounting pads or decorative logos, using an industrial cutting tool called a die. These tapes save assembly time by providing a custom, ready-to-use bonded component for each design.
It is a fully preformed bonded component designed for quick and clean integration.
How Die-cut Tape Works
The die-cutting process involves:
1. Design engineers create a digital template based on the customer's desired shape.
2. Die fabrication - steel dies (flat or rotary) are manufactured to match the shape.
3. Cutting Process:
• Flatbed die cutting: The die is pressed vertically into the tape sheet - ideal for thicker materials and small batches.
• Rotary die cutting: The tape roll is passed through a rotating cylindrical die for high-speed, high-volume production.
Cutting creates a fully formed bonded component, which is then separated from the stock and stored on rolls, sheets or pads ready for assembly.
Die-cut Tape Benefits
Die-cut tape offers significant advantages over manually applied tape rolls:
1. Accuracy & Consistency
Precise part-to-part repeatability with tolerances down to microns – critical in electronic or gasket applications.
2. Efficiency & Labor Savings
Reduces worker time because no cutting or measuring is required. Some manufacturers save more than $200,000 per year by automating die-cutting.
3. Material Match & Functionality
Custom designs use the right adhesive/insert for the application – high temperature resistance, low residue, cushioning, EMI shielding – and avoid misapplication.
4. Reduced Waste
No excess overlap or scrap – increased material yield, less scrap – improved environmental and cost-effectiveness.
5. Ease of Use
Can integrate labels or liners for quick assembly and residue-free peeling.
Typical Materials and Tape Types
Die-cut tapes are commonly used for:
• PSA backing foam (EPDM, polyurethane) - shock-absorbing gaskets
• Double-sided tapes - mounting pads, displays, logos
• Kapton and high-temperature films - electronic insulation
• Low-tack carrier tapes - temporary masking, die-cutting processes
• Rubber/solvent-based PSA - heavy-duty bonding
• UV-cured or water-soluble dicing tapes - semiconductor wafer dicing
Processors work with manufacturers to match tape type, thickness, shape, pressure sensitivity, and environmental durability.
Industry Applications and Actual Cases
1. Electronic Manufacturing
Heatsinks, insulation gaskets, and display brackets rely on micron-level precision and stable pressure-sensitive adhesives.
Dicing tapes secure wafers during dicing and can be stripped with UV light to avoid residue - critical for semiconductor processes.
2. Automotive Assembly
Custom gaskets for bonding logos and interior trim benefit from flexible, high-performance adhesives.
Die-cut forms with labels simplify worker operations.
3. Medical Devices
Tip shapes such as wound dressings, sensors, and catheters require clean removal and biocompatible pressure-sensitive adhesives.
4. Building & HVAC
Tape seals for panels and insulation are precisely cut to ensure consistent compression and weatherproofing.
Die-cutting significantly reduces installation trimming time.
5. Packaging & Branding
Branded tape strips or tear strips (e.g., Easy-Tear Tape) are pre-die-cut for ease of use.
Low-residue options are key for consumer packaging.
Common Challenges & Best Practices
A. Material-Adhesive Compatibility
Mismatched adhesives and substrates (e.g., low surface energy plastics) can lead to premature failure. Surface preparation or corona treatment may be required.
B. Die Wear & Cleanliness
Resin and adhesive buildup dulls die edges—leading to ragged cuts. Routine die cleaning and lubrication are essential.
C. Liner Handling
Inaccurate liners wrinkle during kissing cuts, causing misalignment. A thicker liner simplifies peeling and punching but must unwind properly.
D. Heat & Pressure Control
Excessive slicing or temperature causes adhesive bleeding or tape distortion—especially with sensitive PSAs. Equipment calibration is key.
E. Electrostatic & Dust Control
Static builds on synthetic tapes, attracting contaminants. Anti-static systems or dust-free environments maintain precision.
Best‑Practices Guide for Die‑Cutting Tape
1. Start with a precise digital pattern – CAD-ready templates for 100% accuracy.
2.Choose the correct die – flatbed for flexibility, rotary for volume. Use hardened steel dies.
3. Select appropriate tape – balance adhesive, backing, liner, and functional additives.
4. Ensure clean, temperature-controlled environment – 20–25°C preferred to reduce adhesive creep.
5. Schedule regular die maintenance – clean adhesive buildup, check liner quality, monitor wear.
6. Use proper pressure settings – tailored to tape thickness and material.
7. Include tabs or extended liners – for ergonomic peel-off and contamination control.
8. Perform first article inspection (FAI) – verify dimensional accuracy and adhesion before full-scale runs.
9. Train staff on peel mechanics – liner removal without lifting edges.
10. Track usage and scrap – review shot-to-part ratios and adjust for waste reduction.
Conclusion
Die-cutting tape bridges engineering design with efficient assembly. By transforming PSA rolls into custom-shaped components, manufacturers enhance precision, reduce waste, and streamline production. Successful implementation depends on selecting the right materials, maintaining clean dies, calibrating equipment, and training operators.
With projected wafer sizes shrinking in semiconductors, automotive electrification, and medical device miniaturization, the precision and adaptability of die-cut tape remain essential for scalable manufacturing.
If you'd like, I can create a downloadable infographic, or tailor this into a landing page or technical white paper with embedded product specs—let me know!
Keyword:
die-cutting tape,custom adhesive components,tape die-cutting benefits
RELATED NEWS